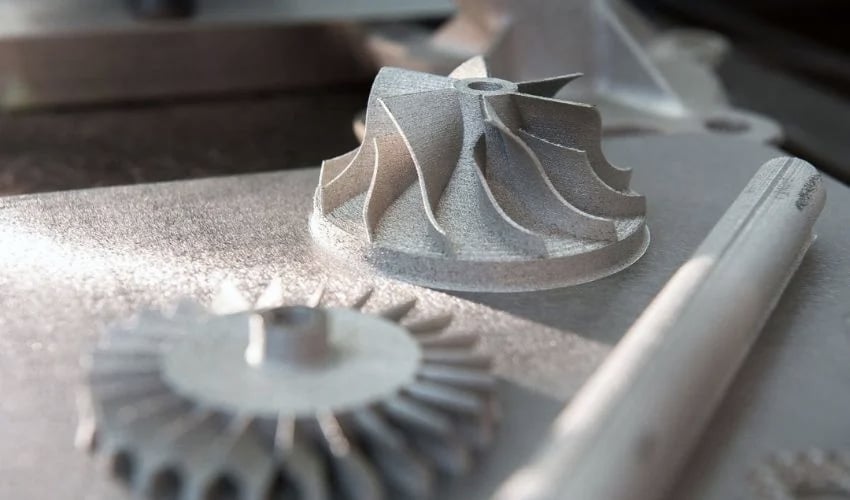
Le NIST pourrait améliorer l’adoption de l’impression 3D métallique à grande échelle
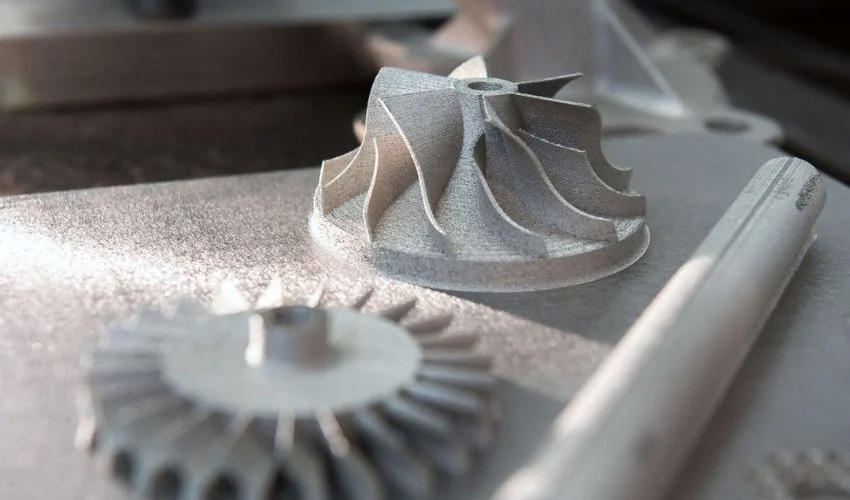
L’un des plus grands obstacles à l’adoption généralisée de l’impression 3D métallique est qu’il existe encore de grandes lacunes dans la compréhension de ce qui arrive au matériau au cours du processus. Plus précisément, il existe peu d’outils qui peuvent montrer ce qu’il advient de la structure interne de différents métaux lorsqu’ils sont fondus puis solidifiés lors de l’impression. Cependant, ce problème pourrait appartenir au passé. L’Institut national des normes et de la technologie (NIST), l’Institut royal de technologie KTH en Suède et d’autres institutions ont annoncé une avancée dans la capacité de prédire et de contrôler les caractéristiques des pièces métalliques imprimées en 3D. Cela pourrait permettre de rendre l’adoption de l’impression 3D métallique plus facile pour la fabrication à grande échelle.
Ce n’est pas la première fois que le NIST s’intéresse à l’impression 3D métal. L’année dernière, peu de temps après que l’administration Biden ait lancé l’initiative AM Forward, l’institution a accordé environ 3,7 millions de dollars de subventions pour surmonter les obstacles actuels et futurs à l’adoption de la fabrication additive métallique. Ces projets se sont concentrés sur des sujets tels que la détermination des propriétés des matériaux clés pour le contrôle de la qualité dans le secteur.
Se tourner vers le passé pour améliorer l’impression 3D métallique à l’avenir
La nouvelle fait suite à une autre annonce de la NASA selon laquelle elle étudierait davantage les moyens d’améliorer la certification et la qualification des pièces métalliques imprimées en 3D. L’impression 3D ne fait que gagner en popularité grâce à ses avantages en termes de réduction des coûts et de déchets. Cependant, les problèmes liés à la qualification et à la cohérence continue des propriétés des pièces ont rendu difficile une adoption encore plus large. Le NIST espère que cette découverte pourrait changer cela, car elle accordera ce qu’ils considèrent comme un niveau de maîtrise sans précédent sur l’impression 3D métallique. Et pour ce faire, ils se sont tournés vers le passé.
Les scientifiques savaient que pour garantir les propriétés des matériaux, il fallait mieux comprendre ce qui se passait pendant les taux de fusion et de refroidissement du métal dans le processus d’impression. Plus précisément, ils devaient comprendre comment les vitesses de refroidissement du métal influencent la structure de la pièce. Cependant, cela s’est avéré difficile à faire car la solidification se produit presque instantanément, ce qui rend presque impossible l’investigation. Pour contourner ce problème, les chercheurs ont utilisé deux accélérateurs de particules différents pour observer la structure interne de l’acier lors de sa fusion puis de sa solidification lors de l’impression 3D. Des rayons X ont ainsi été générés par les accélérateurs de particules du laboratoire national d’Argonne et de l’Institut Paul Scherrer. Ils étaient suffisamment puissants pour capturer des images des processus, en testant le taux de températures allant de dizaines de milliers à plus d’un million de kelvins par seconde.
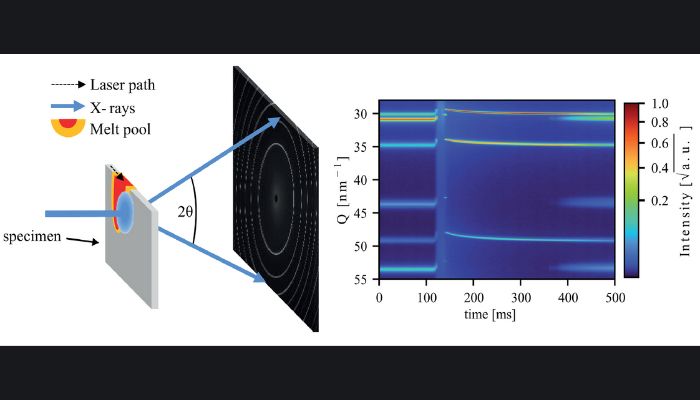
Ces résultats ont ensuite été comparés à un modèle informatique développé dans les années 80 qui décrit la solidification des alliages. Ce retour vers le passé n’a pas été fait sans raison. Ce modèle est réputé pour prédire les propriétés des matériaux dans les processus de fabrication traditionnels, mais jusqu’à présent, il n’était pas sûr qu’il soit applicable à la fabrication additive métallique compte tenu des changements rapides de température pendant l’impression. Les chercheurs ont alors découvert que ce qu’ils avaient observé était également prédit dans le modèle. Le modèle informatique a été un outil fiable pour la conception de matériaux dans la fabrication traditionnelle et il semble maintenant qu’il pourrait être utilisé pour l’impression 3D. Le communiqué de presse mentionne que le modèle pourrait être utilisé pour informer les scientifiques et les ingénieurs sur les taux de refroidissement nécessaires pour les premières étapes de solidification du processus d’impression. Cela garantira que la structure optimale apparaîtra dans le matériau souhaité, ce qui rendra l’impression 3D métallique plus fiable dans l’ensemble.
Le physicien du NIST, Fan Zhang, co-auteur de l’étude, a conclu : « Fondamentalement, si nous pouvons contrôler la microstructure au cours des premières étapes du processus d’impression, nous pouvons alors obtenir les cristaux souhaités et, en fin de compte, déterminer les performances des pièces fabriquées de manière additive. Le modèle et les données expérimentales sont bien en accord. Quand nous avons vu les résultats, nous étions vraiment excités. Si nous avons des données, nous pouvons les utiliser pour valider les modèles. C’est ainsi que vous accélérez l’adoption généralisée de la fabrication additive à usage industriel. Vous pouvez en savoir plus dans le document de recherche publié dans Acta Materialia ICI.
Que pensez-vous de cette recherche du NIST ? Pensez-vous que la fabrication additive métallique sera encore plus largement adoptée par l’industrie ? Partagez votre avis dans les commentaires de l’article.
*Crédits photo de couverture : Laboratoire de recherche de l’armée CCDC